Your cart is currently empty!
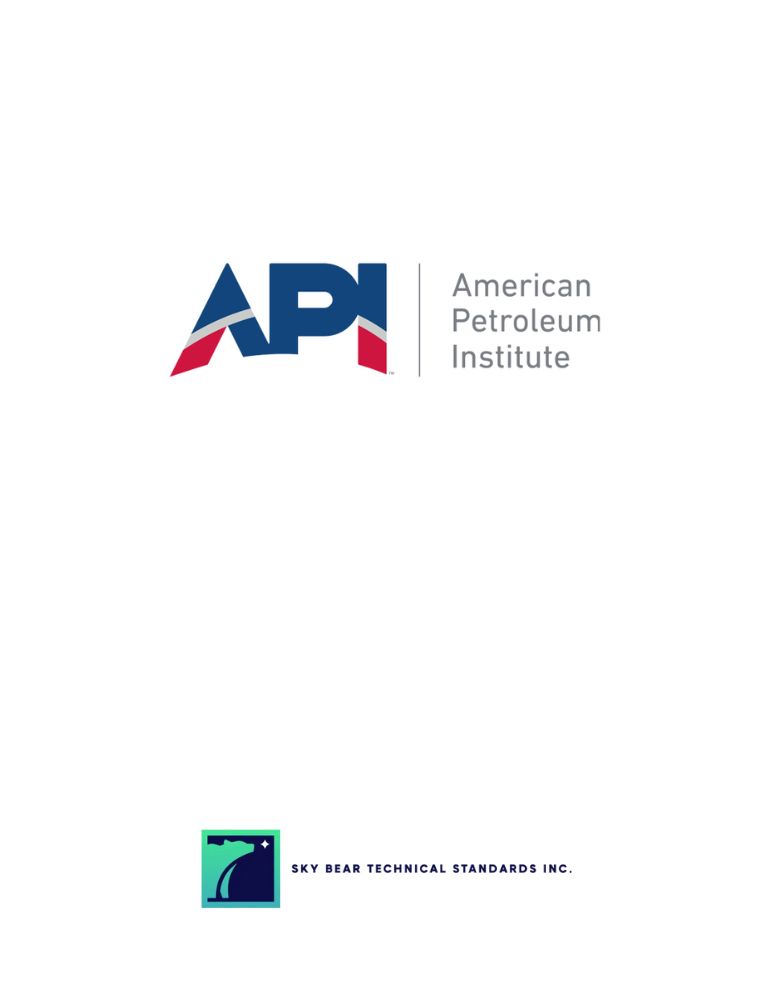
API TR 579-A
API Technical Report 579-A : Development of FEA-based Reference Stress Solutions for Level 2 and Level 3 Crack Assessments
CDN $189.00
This publication was last reviewed and confirmed in 2025.
Description
This research study provides background information that may be used to revise the Fitness-For-Service (FFS) document, API 579-1/ASME FFS-1 2021 (aka “API 579”), more specifically the Part 9 Level 2 Assessment, along with a new Level 3 option for Part 9.
The Part 9 Level 2 crack-like flaw FFS procedure relies on the Failure Assessment Diagram (FAD) approach, which is the most widely used crack assessment methodology in the world. Several industry standards for crack assessment implement the FAD approach, including BS 7910 from the British Standards Institute and the R6 document from the British nuclear power generation industry.
The FAD approach was first introduced in 1976 as a simple approximation for fracture stability assessment of structural components that experience plastic deformation prior to failure. Modern industry standards use improved versions of the FAD, but the approach still contains approximations and simplifications.
The main purpose of the present work is to remove some of the approximations in the existing Part 9 Level 2 FAD procedure and thereby improve accuracy. A side benefit of this work is a new Level 3 option that is even more accurate than the improved Level 2 procedure. This study includes a large number of 3D elastic-plastic Finite Element Analyses (FEA) of components with cracks.
Edition
1
Published Date
2025-05-03
Status
Current
Pages
131
Format 
Secure PDF
Secure – PDF details
- Save your file locally or view it via a web viewer
- Viewing permissions are restricted exclusively to the purchaser
- Device limits - 3
- Printing – Enabled only to print (1) copy
See more about our Environmental Commitment

Abstract
This research study provides background information that may be used to revise the Fitness-For-Service (FFS) document, API 579-1/ASME FFS-1 2021 (aka “API 579”), more specifically the Part 9 Level 2 Assessment, along with a new Level 3 option for Part 9. The Part 9 Level 2 crack-like flaw FFS procedure relies on the Failure Assessment Diagram (FAD) approach, which is the most widely used crack assessment methodology in the world. Several industry standards for crack assessment implement the FAD approach, including BS 7910 from the British Standards Institute and the R6 document from the British nuclear power generation industry. The FAD approach was first introduced in 1976 as a simple approximation for fracture stability assessment of structural components that experience plastic deformation prior to failure. Modern industry standards use improved versions of the FAD, but the approach still contains approximations and simplifications. The main purpose of the present work is to remove some of the approximations in the existing Part 9 Level 2 FAD procedure and thereby improve accuracy. A side benefit of this work is a new Level 3 option that is even more accurate than the improved Level 2 procedure. This study includes a large number of 3D elastic-plastic Finite Element Analyses (FEA) of components with cracks.
Previous Editions
Can’t find what you are looking for?
Please contact us at:
Related Documents
-
API RP 10B-6: Recommended Practice on Determining the Static Gel Strength of Cement Formulations
CDN $121.87 Add to cart -
API RP 1145: Preparation of Response Plans for Oil Spills from Offshore Facilities
CDN $235.40 Add to cart -
API RP 100-2: Environmental Aspects Associated with Exploration and Production Operations including
CDN $176.97 Add to cart -
API RP 11BR: Recommended Practice for the Care and Handling of Sucker Rods
CDN $203.68 Add to cart